Although wire harness assembly is so integrated as PCB, we still need it in some special fields and cases. So today let’s going to know what it is and how to make it.
Wire Harnessing
First of all, we should understand what is wire harnessing. The wire harness is an integrated electrical component, which composed of multiple wires, optical fibers, and insulating materials. The invention of wire harness solves the problem of complex connection of multiple wires, especially in connection of small current and low voltage electrical.
Wire Harness vs Cable Assembly
Somebody also recalls cable assembly when mentioning wire harness, but, to be precise, they are not completely the same. Although both cables and harnesses are used for power transmission, there are obvious differences in application, structure, and appearance. For example, the cable also has a fixed size and construction, while the harness allows flexibly configured based on special requirements. Moreover, cables typically have only one connector, and harnesses have multiple connectors.
Wire Harness Design | Automotive Wire Harness
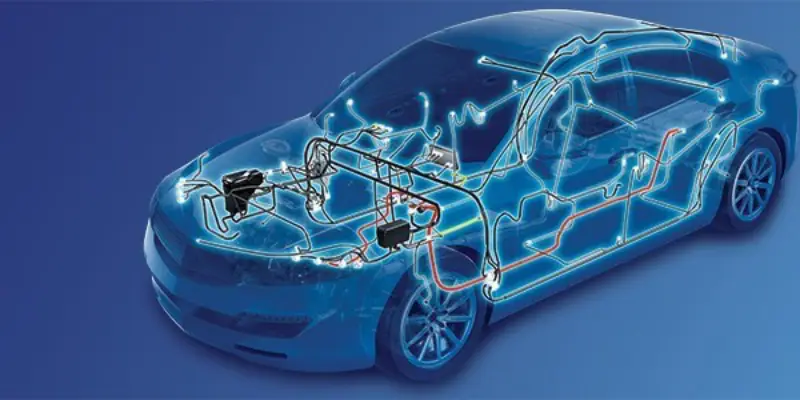
When we want to assemble wire harness, we can get started from wire harness design. Take automotive wiring for example, you should take the following factors into consideration to ensure good construction and effective operation of the whole design.
First, ensure circuit safety by proper arrangement towards the fuse. A fuse can not only protect one circuit but also others. What should be noticed is that only circuits with the same quality can share one fuse and that it is improper to share one fuse between inductive-loading and resistive-loading circuits. Additionally, the fuse in the electronic unit circuit should not be engaging in other circuits at the same time. Last but not least, we advise that actuators or sensors controlled by one electronic unit do not share the same fuse of common circuit.
Second, when we design wire harness assembly, try to keep the wire short, instead of detouring, to the battery.
Third, if we handle wire harness assembly for some devices with high loading to the battery, like air flow meter and throttle valve, it would be better to connect them individually. This will effectively reduce mains fluctuation. In contrast, we can split the routine at the node when designing device with low mains fluctuation such as lighting device and cigarette lighter. This will greatly reduce wire resistance, cost and weight.
Fourth, rationally arrange your grounding which is shared by different circuit, too.
Fifth, adopting shielded wire and twisted-pair wire brings stable and proper signal transmission,especially when dealing with crankshaft position sensor and knock sensor.
It is necessary to link shielding layers to the grounding of the circuit unit. For twisted-pair wire, it is useful to know that the twist amount depends on the type of signal.
Wire Harness Assembly Process
Next, we are going to assembly wire harness based on the design.
- Make the wiring harness material number and match the positioning plate. Ensure that the size of the material number matches the positioning plate so as to avoid waste.
- Wiring. Lay each material with its number on the positioning plate according to the design drawing. When wiring, material with sub-number should be placed in an area first, and then the cross-area placement.
- Insert the PIN and tie the cable. A TER without a PIN should be inserted into the corresponding connector in advance. When tying, the rope should be moved vertically from the bottom of the tie loop.
Wire Harness Testing
Don’t forget to test and inspect your products for quality assurance.
- Electrical inspection. Test data must be strictly checked and confirmed by PE&QE.
- Product inspection. Whether terminals and CONN are within the tolerance zone, whether the binding ring is uniform, and whether the component assembly method is correct are there basic inspection project to ensure good product quality.
- Install the connector and make a final test for debugging.
Custom Wire Harness Assembly
If you are want batch products for your brand business, customizing wire harness assembly is a dispensable step. The first thing we would like to remind you is that choosing a good suppliers is very important. After making clear what your require, you can not only make inquiry to several suppliers for comparison, but also make a site visit to know their R&D ability as well as quality control management. What’s more, clear expression of your demand is very important to shorten the product development period. If possible, equipping yourself with electronic basic knowledge is very useful when you engage in the developing process.
Wire Harness Assembly Manufacturers Top 3
In addition to above consideration, choosing a good supplier for your products is priority things. Here we highly suggest three great factories sophisticated in wire assembly.
Dongguan Jiafu Automobile Accessories Co., Ltd
Jiafu mainly offers wire harness for engine, amplifier, automotive lighting. It is located at Guangdong, China, targeting North America market, China market and Ocenla. With 12 years experience, it wins wide popularity and good reputation in electronic field online.
Moko Technology Ltd.
Moko Technology have abundant 17-year-experience at electronic manufacturing. It is based on Shenzhen, China, and very good at cable & wire harness assembly. Offering on-stop service including wire harness assembly design, component sourcing, wiring, and testing, it is capable of handling medical equipment, telecommunication, automotive and electronics wiring. Last but not least, this factory has built up ISO9001 quality system to ensure product quality. Contact them if you need.
Kunshan Rcd Electronics Co., Ltd.
Kunshan Rcd is a technical factory focusing on customizing antenna and wire harness processing. It also have trade background of North American business and even western Europe. It provides not only cable, such as water proof cable and network cable, and cable assembly processing.